NDT неразрушающий контроль - методы и оборудование
NDT неразрушающий контроль – это уникальная в своем роде методика обнаружения дефектов материалов и конструкций, в ходе которой могут применяться следующие методы:
- метод ультразвукового контроля (УЗК);
- оптический (лазерный) метод;
- радиографический метод.
Каждый из перечисленных методов NDT неразрушающего контроля имеет как преимущества, так и недостатки, при этом, для обнаружения и оценки конкретных дефектов некоторые методы контроля подходят лучше, чем другие. В частности, размеры, ориентация и местоположение дефектов в материале, которые считаются вполне приемлемыми для одной отрасли промышленности, могут быть совершенно неприемлемыми для другой отрасли. Как правило, критерии оценки качества продукции определяются промышленными стандартами (в некоторых случаях государственными или международными), кроме того, клиенты зачастую предъявляют и свои собственные требования.
Выбор подходящего метода напрямую зависит от контролируемого материала, типа или природы дефекта, его местоположения, размера, а также скорости контроля.
NDT неразрушающий контроль – ультразвуковой метод
Метод оценки материалов с использованием ультразвука базируется на передаче акустических волн внутрь контролируемого материала, что позволяет осуществлять контроль любого материала, способного передавать механические вибрации. Ультразвук определяет целый ряд как нелинейных, так и линейных дефектов, одновременно позволяя проводить трехмерное измерение дефекта, при этом, ориентация дефектов может быть поперечной, наклонной или продольной. Читать подробнее.
Основные особенности оптического (лазерного) метода
Оптический метод измерения размеров изделий с использованием лазеров также принадлежит к числу бесконтактных методов NDT неразрушающего контроля, при котором все измерения могут производиться как в отражающем, так и в неотражающем режимах. Подробнее.
Радиографический метод NDT неразрушающего контроля
Радиографический NDT неразрушающий контроль предполагает использование источника проникающего излучения, размер которого регистрируется усилителем изображений или на листе радиографической пленки во время прохождения через контролируемое изделие. Читать далее.
Оборудование для неразрушающего контроля в компании «Norteks»
NDT TechnologiesInc. – это ведущий производитель автоматических систем измерения и неразрушающего контроля. Компания осуществляет разработку, изготовление, установку и обслуживание автоматических систем неразрушающего контроля качества изделий с использованием вихретока, ультразвука и лазеров.
Холдинговая компания «Norteks» является официальным представителем компании NDT TechnologiesInc. в России.
Мы поставляем исключительно оригинальное оборудование NDT для неразрушающего контроля, которое полностью соответствует всем существующим нормам и стандартам качества и специально сконструировано, чтобы удовлетворять потребности каждого клиента в сфере транспортной, нефтехимической, аэрокосмической, ядерной, полимерной, легкой, тяжелой и обрабатывающей промышленности.
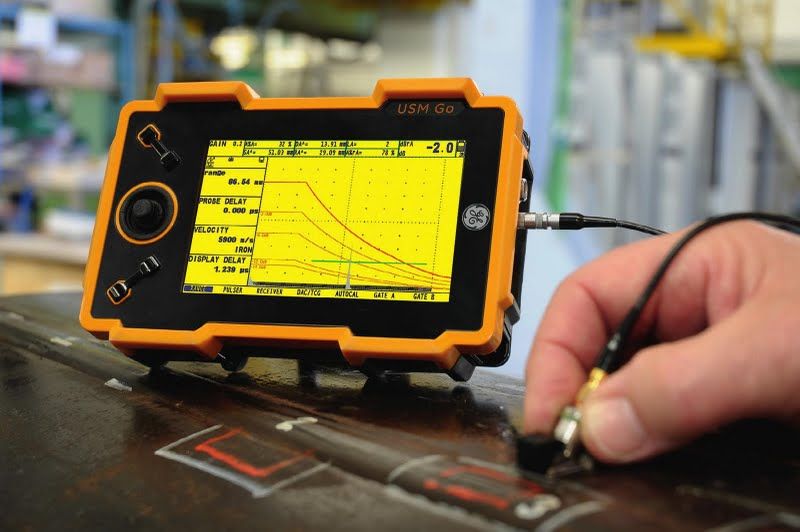
Оборудование
Готовое комплексное решение
Вы обозначаете задачу, мы обеспечиваем комплексное её решение!
Мы делаем все: от исследований и разработок до производства и установки. Кроме того, мы обеспечиваем обучение и техническую поддержку.
Исследования NDT неразрушающий контроль
Постоянные исследования в области науки о материалах, звуковой, оптической и электромагнитной технологий обеспечивают надежную основу для разработки и внедрения все более совершенных систем неразрушающего контроля качества материалов и изделий.
Интеграция систем
Компания NDT Technologies Inc. интегрирует комплексные пневматические гидравлические системы, механическое управление и робототехнические системы.
Мы предлагаем оборудование по испытанию материалов и измерительные программы нашим клиентам в области сталелитейной, транспортной, аэрокосмической, атомной, нефтехимической промышленности, промышленности производства пластмасс, области производства энергии и фабричного производства.
Портативное оборудование
Ультразвуковое
- Измерительный прибор коррозии
- Измерительный прибор толщины
- Детекторы дефектов
- Датчики и вспомогательные средства
Команда
Наши сотрудники могут не только принимать решения на самом высоком научно-техническом уровне, но и нести за них полную ответственность перед клиентом.
Работа всей компании направлена на то, чтобы оправдать ожидания заказчиков. Мы сосредоточены на достижении результатов посредством применения передовых технологий, высококачественного обслуживания и командной работы наших экспертов. Успех, который мотивирует работу наших сотрудников, становится ключевой движущей силой для удовлетворения высоких требований наших заказчиков. Мы гордимся тем, что предоставляем нашим клиентам решения, которые удовлетворяют их потребностям и повышают технические требования к контролю.
Команда профессионалов NDT Technologies Inc отобрана за их обширный опыт и знания. Мы сосредоточены на достижении результатов посредством исполнения инновационных идей. Наша уникальная способность объединять технологии, организации проектов, концептуального проектирования, и методов испытания материалов позволяет нам быстро реагировать на новые разработки в сфере оценки материалов и контроля изделий. Это гарантирует использование передовых технологий в нашем оборудовании и проектах.
Наши инженеры стремятся получить полное понимание особенностей материала заказчика, осуществляя тесное взаимодействие с отделами контроля качества клиента. Эта информация, вкупе с нашей возможностью обеспечивать собственную разработку специализированных ИС и изготовление специальных измерительных преобразователей, датчиков и высококачественных катушек, позволяет нам превзойти требуемые технические параметры любого проекта.
Исследования и разработки
Исследования и разработки, проводимые нашей компанией, ставят нас на голову выше наших конкурентов.
Системы NDT Technologies Inc. совмещают в себе новейшие технические разработки, запатентованные конструкторские особенности и инновационный инжиниринг.
Некоторые из наших технологий способны полностью оценить только эксперты. Хорошим примером служат наши запатентованные Волоконно-Оптические Линии Связи (ВОЛС) для передачи критических сигналов. ВОЛС способны передавать чистые аналоговые сигналы на большие расстояния без искажения.
Использование ВОЛС гарантируют работу нашего оборудования без электронных шумов даже в самой сложной производственной среде. Наше оборудование можно устанавливать без опасения помех, даже рядом с типичными источниками электромагнитных помех: таких, как закалка ТВЧ или высокочастотными сварочными аппаратами.
Многие наши технологии заслуженно признаны поистине замечательными достижениями в области контроля качества материалов.
Назовем некоторые из них:
- RheoSonic ™ – Ультразвуковая система контроля свойств материала. Передовая технология для проведения текущего контроля реологии полимеров. Выпускается серийно для применения в области полимеров. В настоящее время ведутся разработки установок для применения в области переработки продуктов, экструзии металла и литья под давлением.
- Iceye ™ – система контроля и предупреждения об обледенении на воздушных судах. Ультразвуковая технология для обнаружения обледенения на крыльях воздушного судна.
- Brake Liner Testing – Выдающаяся технология для контроля фрикционного материала без применения акустической контактной среды.
Качество, инновация и технология. Вы ставите задачи – мы их решаем!
Миссия
NDT Technologies Inc. работает для того, чтобы обеспечить решение комплексных задач по обеспечению контроля качества выпускаемой продукции.
- Мы учитываем любые требования заказчика, проводим обучение, оказываем послепродажное обслуживание и техническую поддержку в процессе эксплуатации оборудования.
- Мы обеспечиваем самый высокий уровень качества продукции и услуг, чтобы заслужить доверие и уважение наших клиентов.
- Мы соблюдаем высокие этические стандарты, согласующиеся с нашими обязанностями по отношению к обществу, клиентам, сотрудникам и окружающей среде.
- Мы боремся за превосходство, творчество и инновации в области науки.
Проекты
Ниже приведен неполный список проектов, осуществленных нами в Канаде и за рубежом:
- Canadian National Rail (CN)
- Ontario Hydro
- Ipsco
- Welland Pipe
- Wolverine Tube
- Holden International
- Trinec Steel Works
- Huta Katowice
- Bonatrans
- Tex-Tube
- Lone Star Steel • Angang
- BaoGang
- Shanghai 5
- Baotou
- Jigang
- Ma Steel
- Bhilai Steel Plant (BSP)
- Steel Dynamics (SDI)
- Cofab Brasil
- TRW
Членство в компаниях
NDT Technologies Inc. является членом/продукция компании соответствует стандартам/ следующих организаций:
- CGSB –Canadian General Standards Board (Комитет Канады по Стандартизации)
- CINDE – Canadian Institute for NDE (Канадский Институт Технологий Неразрушающего Контроля)
- Chambre de Commerce Quebec – Торговая Палата Квебека
- Canadian Railroad Association – Канадская Ассоциация Железных Дорог
- Ultrasonic Industry Association (UIA) – Промышленная Ассоциация Ультразвука
- ASTM – American Society of Testing Materials (Американское Общество по Испытаниям Материалов)
- ASNT – American Society for Nondestructive Testing (Американское Общество Неразрушающих Испытаний)
- ASM – American Society for Metals (Американское Общество Металловедения)
- Tube and Pipe Association (TPA) –Ассоциация Производителей Трубной Промышленности
Где применяют неразрушающий контроль?
Транспортная промышленность
Компания NDT много лет успешно работает в области транспортного машиностроения, поставляя самое современное оборудование для автоматического контроля качества различных деталей и узлов ответственного назначения.
В широкий перечень таких изделий входят как железнодорожные колеса и рельсы, так и автозапчасти и детали аэрокосмического применения.
Аэрокосмическая промышленность
Аэрокосмическая промышленность
Мы предоставляем технику, производимую под заказ, для осуществления автоматического контроля в области аэрокосмической промышленности, как то: контроль композиционных материалов, оценки повреждений от коррозии и обнаружение трещин.
Контроль деталей из композиционных материалов
Компания NDT Technologies Inc. является ведущим производителем контрольного оборудования для композиционных материалов в аэрокосмической промышленности. Вращающиеся лопасти вертолета и авиационные крылья могут иметь дефекты невидимые невооруженным глазом. Наше современное ультразвуковое оборудование позволяет обнаружить их и получить подробную информацию о происхождении данных дефектов.
Ниже предоставлен пример индикатора с-типа композитного клина.
Красные области указывают на повреждение материала.
Устройства определения толщины лакокрасочного покрытия
Внизу приведен пример тестирования методом вихревого тока, где толщина краски авиационного крыла определяется в виде цветного кода. Минимальная толщина указывается в зеленом цвете, максимальная толщина в темно-голубом.
Заклепки отчетливо просматриваются в виде круглых или овальных точек.
Автомеханика
Автомеханика
Мы предоставляем технику, производимую под заказ, для автоматизированного контроля торсионов, направляющих обшивок, тормозных колодок и других деталей автомобилестроения.
Устройство контроля качества изготовления гильз цилиндров
Данная система контроля предназначена для автономного обнаружения внутренних и внешних дефектов в гильзах цилиндров автомобильного двигателя. Система применима для обнаружения микротрещин, поверхностных дефектов и дефектов, находящихся под поверхностью с помощью метода вихревого тока. Кроме того, данная система отслеживает средний уровень шероховатости поверхности и условия термообработки. Поврежденные детали автоматически отбраковываются.
Обычный цикл контроля занимает менее 15 секунд.
Установка контроля качества тормозных колодок при проверке двигателя на стенде (ВТМ)
Высокое качество фрикционных материалов, используемых в производстве автомобильных тормозных колодок, подтверждается посредством автоматизированной проверки, основанной на уникальной ультразвуковой технологии без применения связующего агента. Обычно ультразвуковая передача осуществляется посредством акустического связующего агента, что запрещено при контроле тормозных колодок. Ультразвуковой контроль без связующего агента достаточно сложный процесс. Более того, тормозные колодки производятся из материалов, поглощающих высокий уровень шума, что затрудняет процесс проверки их качества.
Наша новейшая разработка датчиков позволяет успешно осуществлять тестирование посредством «сухого» метода ультразвукового контроля. Три роликовых датчика излучают звуковые волны, которые проникают через любую толщину материала. В случае обнаружения дефекта, проверяемая деталь бракуется. Цикл контроля полностью автоматизирован и оснащен устройством удаления бракованных изделий.
Система разработана для проверки широкого ряда тормозных колодок и составных частей. Наша автоматизированная система для определения внутреннего расслоения и полостей в автомобильных тормозных колодках может быть встроена в производственную линию, или может использоваться автономно.
Устройство контроля торсионных стержней
Полуавтоматическая система предназначена для автономного контроля торсионных стержней посредством метода вихревого тока. Система разработана для определения продольных дефектов в стержнях после формовки и термообработки. Решение принять (отклонить) определяется методом сравнения электрических сигналов в соответствии с размерами дефектов. Устройство способно обнаружить дефекты размером 0,005” (0,12 мм). Данное устройство заменяет стандартный контроль методом магнитного порошка.
Устройство контроля блока двигателя
Данная ультразвуковая система предназначена для автономного контроля ответственных поверхностей установки подшипников в литом блоке двигателя. Контрольное устройство осуществляет проверку посредством рентгеновских лучей для обнаружения плоских дефектов и мелкой пористости. Процесс контроля полностью компьютеризирован и управляет работой целой группы специализированных станков, работающих в одной линии. Результаты контроля отображаются в графическом виде на экране компьютера.
Автоматизированное устройство контроля заготовок
Данная ультразвуковая система контроля предназначена для работы в тяжелых условиях и оснащена загрузочным и разгрузочным оборудованием для круглых заготовок до 800 мм диаметром. Система осуществляет контроль зачищенных и необработанных заготовок на наличие внутренних и поверхностных дефектов с использованием ряда различных датчиков.
Рентгенографическая система
Данная автоматизированная система предназначена для осуществления контроля в режиме реального времени швов тонкостенных (от 1,5 мм) трубопроводов тормозных гидравлических систем и других ответственных, тяжелонагруженных деталей.
Системы контроля других автомобильных деталей
Автомобильные детали могут быть проверены на наличие поверхностных трещин в критических областях, а также на величину закалки материала. Автоматическая система обеспечивает надежные результаты проверки и высокую производительность. Контроль методом вихревого тока может быть совмещен с ультразвуковым контролем для измерения степени шероховатости в определенных местах деталей.
Металлургия
Eddytron™ ERW/8
Для труб со сварным швом методом электро – контактной сварки
Данная надежная система разработана для работы в трубопрокатной промышленности. Система определяет и оценивает продольные, поперечные и сквозные дефекты в трубах со сварным швом методом контактной сварки до 8” (200 мм) в диаметре.
Определение дефектов выполняется посредством динамического вихретокового метода сканирования.
Размеры дефектов электронным путем сравниваются с искусственными дефектами, нанесенными на контрольные образцы (СОПы), в соответствии с утвержденными нормативами.
* Примечание: СОП – стандартный образец предприятия, утвержденный в установленном порядке.
Устройство управляет плавающей контрольной головкой. Данная головка может вращаться вдоль оси, а также как в вертикальном направлении для контроля размера трубы и оценки ее качества.
Трубы с лазерным сварным швом и со сварным швом контактной сваркой на производственной линии контролируются согласно стандартам API, ASME, DIN и другим международным стандартам.
Установка контроля в стандартном исполнении состоит из:
- Измерительного устройства вихревого тока
- Установки испытательной обмотки
- Устройства магнитного насыщения
- Линейный аналого-цифрового преобразователя
- Устройства маркировки дефектов
- Оптического и (или) Акустического устройства записи данных сигнала брака.
Eddytron ™ ERW/4
Для сварных труб из нержавеющей стали
Данная система разработана для контроля сварных труб из нержавеющей стали способом продольно- спирального перемещения одноканального датчика вдоль проверяемого изделия. Материала магнитного насыщения не требуется. Установка оснащена оптической сигнальной системой обнаружения дефекта с одновременной маркировкой места повреждения специальной краской.
Eddytron ™ 2.0
Eddytron™ 2.0 – это автоматизированное устройство вихревого тока для финишного контроля трубного материала. Устройство оснащено приводными подающими и выводящими роликами и разработано для определения поверхностных дефектов в трубах и (или) сплошных стержнях до 4” (100 мм) наружного диаметра. Контролируемые изделия магнитно насыщаются, проверяются на наличие поверхностных дефектов и размагничиваются перед выходом из контрольного устройства. Автоматизированное двухцветное маркирующее устройство классифицирует и определяет глубину дефекта в два этапа. Устройство может быть подсоединено к записывающему устройству или к компьютеру по сбору и обработке данных для обеспечения статистических отчетов.
Rototron ™
Ультразвуковая система контроля Rototron™ c вращающейся испытательная головкой. Изображенная система (справа) разработана для контроля труб или сплошных стержней до 50мм в диаметре. Эта гибкая и универсальная система может быть оборудована и устройством предварительного замера толщины. Устройство включает в себя от 4 до 16 контрольных датчиков. Ультразвуковая иммерсионная дефектоскопия основана на применении заменяемых направленных датчиков, которые настраиваются посредством микровинтов для создания необходимого угла звуковой волны в контролируемых изделиях. Данный метод позволяет включать широкий ряд настроек по желанию заказчика.
SonoTron™
Для круглых стержней
Данная система предназначена для ультразвукового контроля с высоким разрешением круглых стержней (в процессе обработки) на наличие внутренних и внешних дефектов.
Поперечное сечение материала (справа) указывает на типичную трещину, расположенную в центре.
Цветное изображение (слева) отображает результаты ультразвукового контроля на образце стержня длиной 24” (≈ 600 мм). Поврежденные участки помечены красным цветом. Отметка наносится автоматизированной системой контроля, которая объединена с компьютеризированным устройством обработки сигналов. Программное обеспечение дает возможность подсчета приемлемой длины с целью уменьшения затрат материала. Контроль может осуществляться на заранее выбранных участках любого стержня. Более того, определенные участки материала могут подвергаться более тщательному контролю.
Устройство контроля корпусов(Полых тел)
Мы разрабатываем оборудование для контроля стальных и алюминиевых обшивок для корпусов аппаратов высокого давления общего назначения, а также оборонной промышленности.
Наше оборудование обеспечивает высокоплотный объемный контроль изделия в восьми направлениях, что позволяет определять плоские дефекты и отслеживать толщину стенки.
Устройство контроля движущихся деталей
Мы предлагаем лабораторное оборудование для качественного контроля движущихся деталей во время процесса обработки. Набор высокочастотных ультразвуковых преобразователей определяет микротрещины в переходных областях дефицитного материала на длине 30мм движущихся (вращающихся) деталей.
Устройство контроля армированных труб
Контроль биметаллических армированных труб осуществляется посредством комбинации электромагнитного и ультразвукового метода.
Электромагнитный метод применяется при измерении толщины внутренней стенки. Ультразвуковой метод используется при контроле внутренней целостности соединения и определения дефектов в стальных трубах в нескольких направлениях.
Армированные трубы используются для транспортировки химически агрессивных жидкостей.
Устройство контроля проводов
Технология Eddytron™ применяется в проволочной индустрии. Наше устройство определения дефектов методом вихревого тока проверяет провода посредством бесконтактного метода.
Устройство контроля толстолистовой стали
Совмещая метод вихревого тока и ультразвуковой метод контроля, наша система разработана для контроля всей поверхности и объемного покрытия больших листов толстолистовой стали (более 4м в ширину, 50 м в длину) и более 100 мм толщиной. Система определяет и оценивает дефекты расслоения, а также продольные и поперечные дефекты.
Устройство контроля свойств материала с приводом RheoSonic™ Technology
В то время как контроль неоднородности и выявление дефектов посредством ультразвука является нашей специализацией, мы постоянно разрабатываем новые устройства, где можем применить наши знания и опыт в работе с оборудованием неразрушающего контроля изделий и материалов.
Если вы обрабатываете полимеры, формовочные металлы или занимаетесь отливкой, наша запатентованная технология может быть использована для контроля свойств материала на линии в режиме реального времени в процессе производства.
После 20 лет разработок и исследований и 3 лет тестирования Система контроля свойств материала в режиме реального времени впервые доступна любому покупателю.
В системе используется Устройство Контроля Обработки (УКО) – компактное, передвижное и безопасное.
Преимущества для полимерных изделий, полученных методом экструзии, смешивания и инжекционного прессования:
- Встроенное устройство контроля качества
- Снижение отходов и брака
- Максимизация пропускной способности и повышение выхода продукции
- Контроль всего процесса от приемного желоба до выхода из устройства
- Отсутствие ненужных остановок для настроек и проверки корпуса экструдера
- Снижение длительности цикла
Возможность контроля следующих параметров:
- Индекс качества плавки
- Вязкость (Молекулярная масса)
- Деструкция полимеров
- Химическая экструзия
- Экструзия пенопласта
- Износ корпуса инжектора и перемещающегося шнека
- Распределение времен пребывания (по фазам цикла)
- Смесь полимеров
- Концентрация наполнителя
- Распределение наполнителя
- Уровень плавки и смешивания
- Завершение заливки
- Температура формы и детали
- Отвердевание
Преимущества применения контроля с помощью ультразвука:
- Позволяет видеть насквозь корпус экструдера, литейную форму или штамп
- Чувствительность, как к свойствам материала, так и к условиям обработки
- Неразрушающий (не изменяет материал)
- Непроникающий (не возникает помех во время процесса)
- Контроль в режиме реального времени
- Надежный (прочно закрепленные части)
- Устройство доступно в работе и техническом обслуживании
- Экономически целесообразный
- Возможность проводить контроль от загрузочного желоба до выхода из устройства
Как это работает?
- Импульсы ультразвука малой мощности (менее чем 0.1 Вт = неразрушающий) проходят через расплав полимера
- Скорость распространения звука, ослабление, отражающий коэффициент и рассеянные сигналы измеряются в режиме реального времени и зависят от молекулярных, химических и физических свойств материала.
- Любые изменения свойств материала и параметров работы могут быть связанны с колебаниями ультразвуковых свойств
Особенности контроля вязкости и молекулярной массы:
- Производственный процесс разработан для создания показателя уровня реологических свойств.
- Молекулярная масса или вязкость расплава обычно проверяется в автономном режиме
Встроенная система контроля скорости звука во время химической экструзии дает возможность доступа к вязкости и молекулярной массе в режиме реального времени.
Износ корпуса может быть определен при помощи измерения расстояния между термостойким ультразвуковым преобразователем (обозначенный УП на нижнем левом рисунке) и внутренней стенкой корпуса посредством измерения промежутка времени между двумя последовательными эхо отражениями L1 и L2, нижние правые и левые цифры, отраженными от внутренней стенки корпуса.
![]() |
![]() |
![]() |
Схематичная диаграмма измерительного принципа | Выполнение 30 мм двухшнекового экструдера. УП это пьезоэлектрическая пленка смазанная солевым раствором. |
Эхо сигналы, отражающиеся от поверхности внутренней стенки корпуса, создаваемые и получаемые посредством УП, изображенным по середине. |
![]()
|
![]() Устройство определения износа штека |
Варьирующееся время эхо сигналов, отраженных от двух точек (А и В) двухходового шнека за два оборота, показывает четкое отклонение шнека во время процесса экструзии. |
Преимущества контроля в режиме реального времени:
- Встроенное устройство контроля качества
- Снижение отходов и брака
- Повышение выхода продукции
- Отсутствие ненужных остановок для настроек и проверки корпуса
Контроль степени плавления
Возможность ультразвука проникать через полимер в основном зависит от степени плавки последнего. Таким образом, амплитуда ультразвукового сигнала, прошедшего через полимер может быть использована для контроля степени плавления полимера.
![]() |
![]() |
![]() |
Осуществлялся контроль ввода в действие ультазвуковых датчиков в закрытом смесителе и контроль эхосигналов, отражающихся от кромок смесительного полотна | Процесс плавки ПНП (полиэтилен низкой плотности) в закрытом смесителе контролировался при помощи крутящего момента и измерений температуры. | Тот же процесс контролировался одновременно с ультразвуком. Сила ультразвукового сигнала четко определяет начало и конец плавки. |
Контроль процесса формовки и температуры детали
Контроль температуры плавки
Скорость ультразвука при плавке в литьевом отверстии или при формовке может быть использована для измерения температуры плавления в режиме реального времени.
Температура плавления, измеряемая термоэлементом. | Температура плавки, измеряемаяультразвуковыми датчиками. |
![]() |
Контроль давления расплава
Изменение давления расплава может быть определено по изменениям времени прохождения сигнала до цели и обратно ультразвукового эха в ультразвуковом буфере или между внутренней и внешней поверхностями формы.
Отвердевание
Микроформовка
Барабан станка, Оформляющая вставка пуансона и Детали
Ультразвуковой сигнал, отражающийся в барабане/Расплав
Запатентованная технология:
- Ультразвуковые датчики с соединительной деталью типа Dynisco
- Встроенный уменьшенный термостойкий преобразователь
- Отдельный термостойкий преобразователь
Термостойкий ультразвуковой армированный буферный датчик
- Высокий сигнал уровня шума до 60 ДБ в режиме импульсного эха.
- Превосходное распределение продольных и поперечных волн.
- Работа до 900о
- На конце ультразвукового преобразователя (УП) не требуется воздух, вода или охлаждающая жидкость
- Рабочая частота 1-20 МГц
- Механически обработанный корпус
- Без перекрестных помех
Такая же внешняя форма, как и у температурных датчиков Dynisco и датчиков давления;
Легко устанавливается на барабане станка, на выходе экструдера или головке экструдера.
Встроенный уменьшенный термостойкий датчик
- Сигнал уровня шума до 40 ДБ в режиме импульсного эха.
- Средняя мощность сигнала
- Термический диапазон работы до 500о С
- Не требуется связующего агента
- 2-30 МГц рабочая частота и широкий диапазон рабочих частот
- Допускается криволинейная поверхность
- Допускается бессвинцовый материал
Ультразвуковые датчики устанавливаются на внешних поверхностях барабана, формовки или головки экструдера для контроля процесса экструзионного прессования, микроформовки и инжекционного прессования.
Расположение датчиков
Экструзия полимерных изделий и смешивание
(Одношнековый или двухшнековый экструдер или закрытый смеситель)
На выходе
Вдоль барабана
|
![]() 63 мм одношнековый экструдер (FLAG) |
![]() 50 мм двухшнековый экструдер (Leistritz) |
![]() Закрытый смеситель (C.W. Brabender) |
![]() 30 мм двухшнековый экструдер (W&P) |
Инжекционное прессование и микропрессование
Вдоль барабана
На насадках
|
![]() На насадках и пресс-форме |
![]() 150Т Двухкомпонентная Пресс-форма (Engel) |
![]() На внешней поверхности пресс-формы |
![]() Микропрессовочный станок |
Запатентованная технология:
- Многократное использование датчиков
- Индикатор изображения в режиме реального времени
- Хранение и извлечение информации
- Удаленный доступ посредством беспроводной сети
Коммерчески выгодный
Только затраты на оборудование
Надежный
Система DPM
Наша система – это простое устройство, прекрасно адаптированное к экструзии полимерных изделий, включая экструзию пенопласта. Может применяться на выходном отверстии экструдера (в головке) для контроля:
![]() |
|
Многодатчиковая Ультразвуковая Система
Наша система может быть использована для исследования процессов в смешивающей реакционной камере.
Применение:
- Контроль износостойкости
- Распределение времен пребывания (РВП) в барабане
- Смешивание
- Состав материала
- Экструзивная реакция
Характеристики:
- Быстрое получение данных
- Многодатчиковая система
- Удаленный доступ посредством беспроводной сети
- Изображение информации в режиме реального времени
- Адаптирована для контроля процесса инжекционного прессования и экструзии полимерных изделий в барабане.